Smart Factory
Background and challenges
In the context of strict regulatory supervision in industrial safety, workplace compliance management has become the lifeline for the survival and development of enterprises.
However, traditional factory safety management has systematic flaws:
These pain points highlight the excessive reliance of traditional factory compliance management on “human defense”: numerous blind spots in regulation, difficult evidence traceability, and large flexibility in standard implementation, leaving enterprises facing huge fines, production suspension for rectification, and even criminal liability risks in terms of compliance. In the current situation where safety production regulations are continuously tightened, building an “all-time perception – automatic warning – mandatory intervention” proactive compliance system has become an urgent need for industrial intelligence.
Solutions
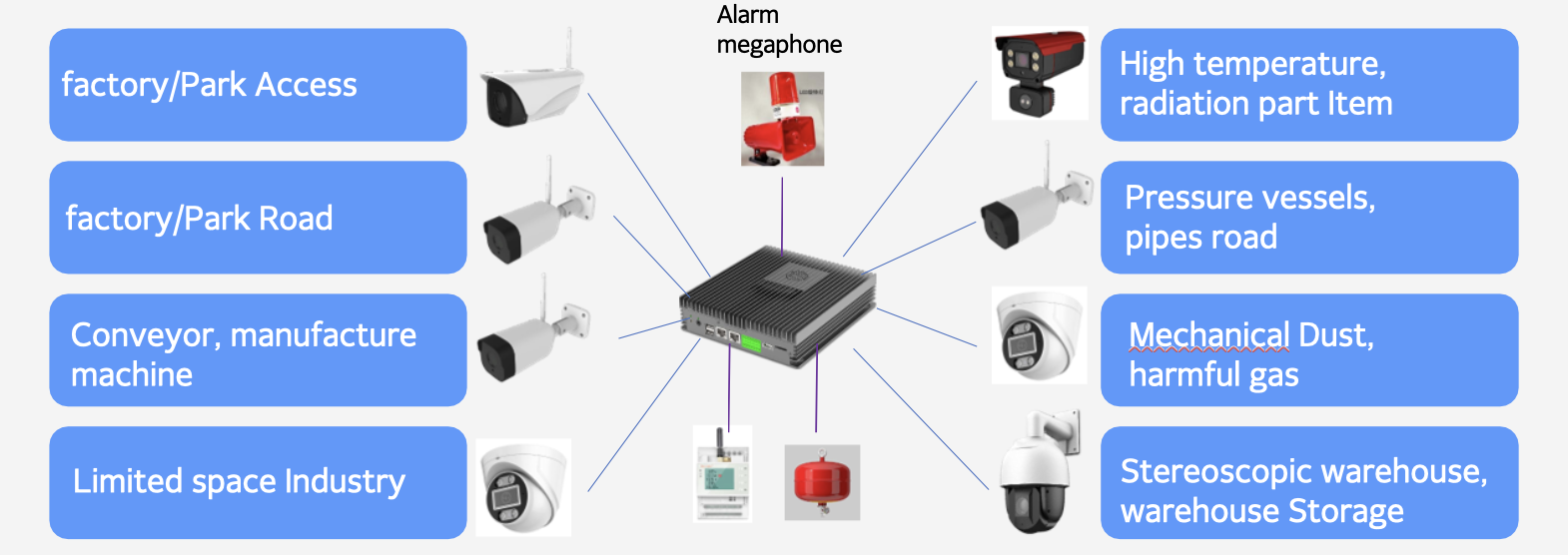
To meet the urgent regulatory needs for industrial safety production, we have restructured the compliance management system with “AI visual rule engine + edge intelligence”, upgrading the traditional passive mode of relying on manual supervision to an active prevention system of “continuous monitoring – automatic correction – closed-loop handling”:
- Compliance risk interception within milliseconds
Behavior recognition algorithm – Real-time analysis of high-risk operations: Automatically identify violations such as not wearing safety helmets, protective gloves, or work clothes in high-temperature/radiation areas; Trigger leakage alarms within seconds in pressure vessel areas; Precisely count the number of personnel in confined spaces and block the accident chain at the source.
Target recognition algorithm – Strengthened control of dangerous areas: Smartly detect illegal intrusions by personnel in hazardous areas such as hazardous chemical storage areas and around moving machinery, and trigger sound and light alarms to disperse them; Automatically capture smoking or illegal fire operations through smoke detection, significantly improving the fire response speed.
- Mandatory compliance execution through edge computing
AI micro servers are deployed locally at key nodes of the production line, completing analysis and triggering control instructions within a short period of time: Automatically suspend equipment operation when protective equipment is not worn; Start emergency broadcasts when personnel are trapped in dangerous areas; Real-time push accountability work orders when the duty room is unattended or sleeping.
- Full-scenario coverage of key risk points
It covers 10 types of high-risk scenarios: from conveying machinery (area intrusion alarm), dust workshops (mask/gloves detection), to fire-fighting facilities (channel occupation recognition), and confined spaces (falling and tripping monitoring).
- Automated construction of compliance evidence chain
All alarm events are automatically associated with time, location and video clips, generating a visual compliance report that meets the traceability requirements. and reduces legal risks for the enterprise.
The value of this plan lies in shifting compliance management from “post-event accountability” to “process control”, resulting in a significant reduction in the violation rate in typical scenarios, a substantial decrease in the rate of production safety accidents, and a concurrent reduction in regulatory penalties and production suspension losses.To meet the urgent regulatory needs for industrial safety production, we have restructured the compliance management system with “AI visual rule engine + edge intelligence”, upgrading the traditional passive mode of relying on manual supervision to an active prevention system of “continuous monitoring – automatic correction – closed-loop handling”:
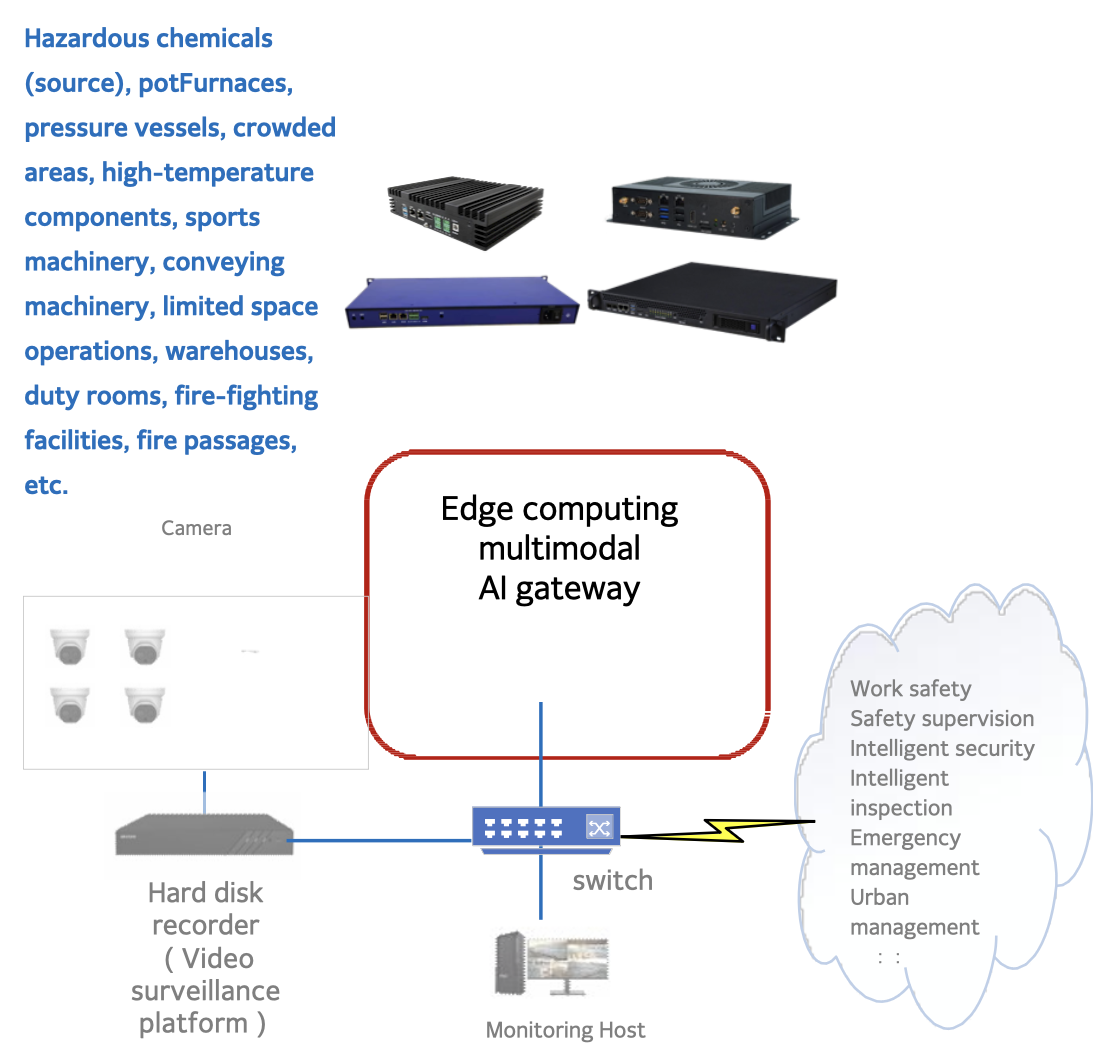
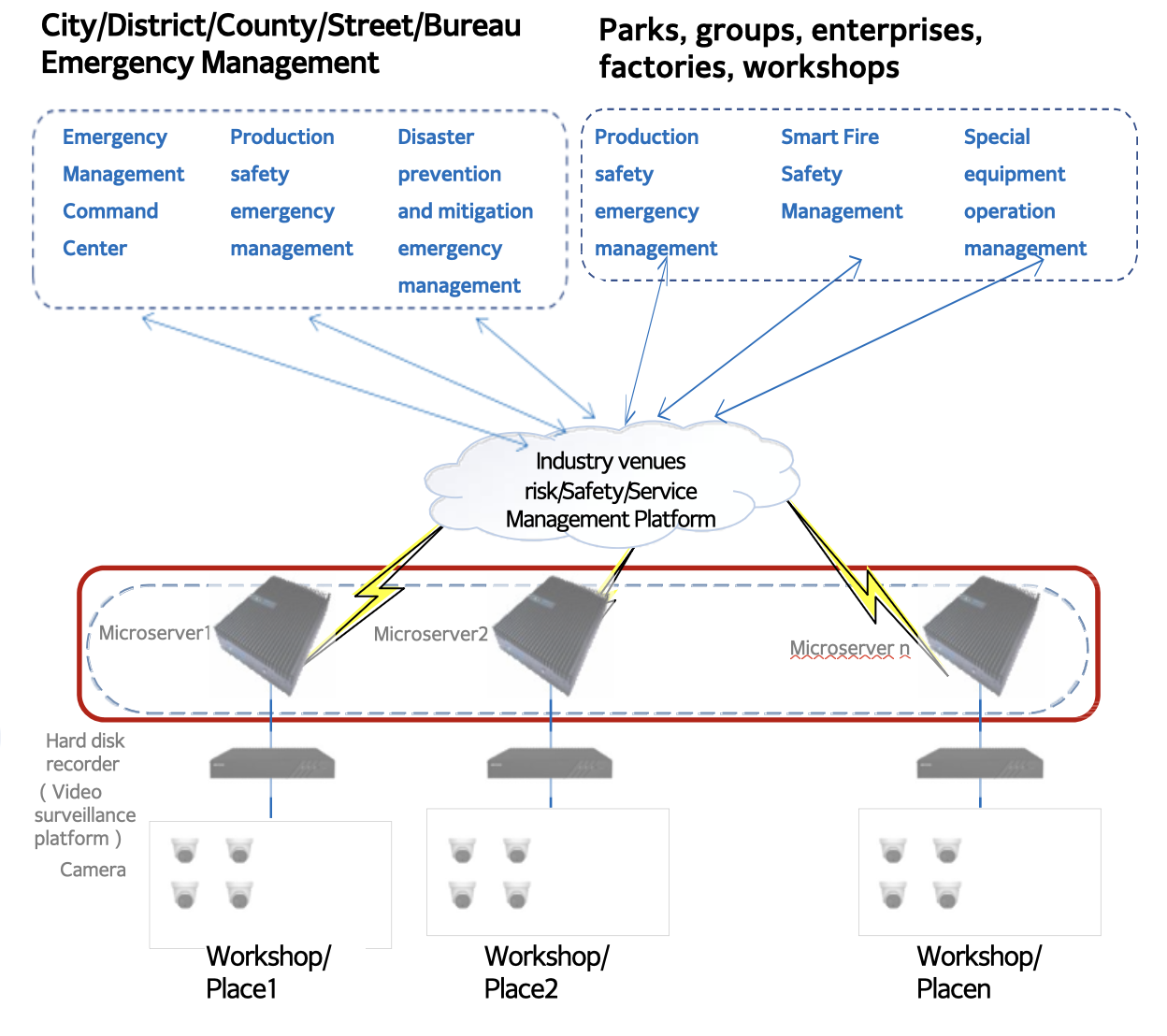
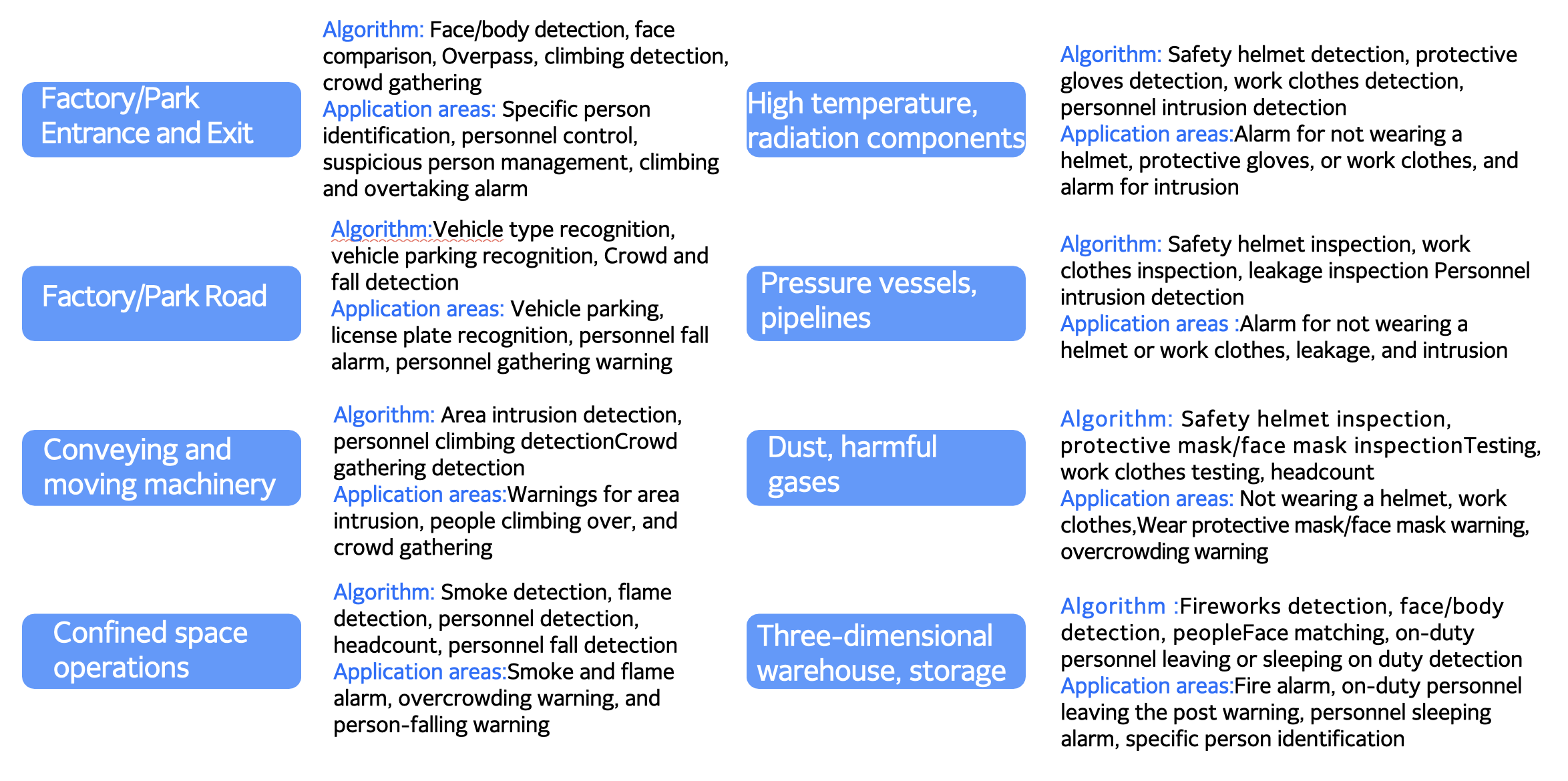
Monitoring Screenshot
This is the recognition image obtained by the intelligent factory monitoring system.
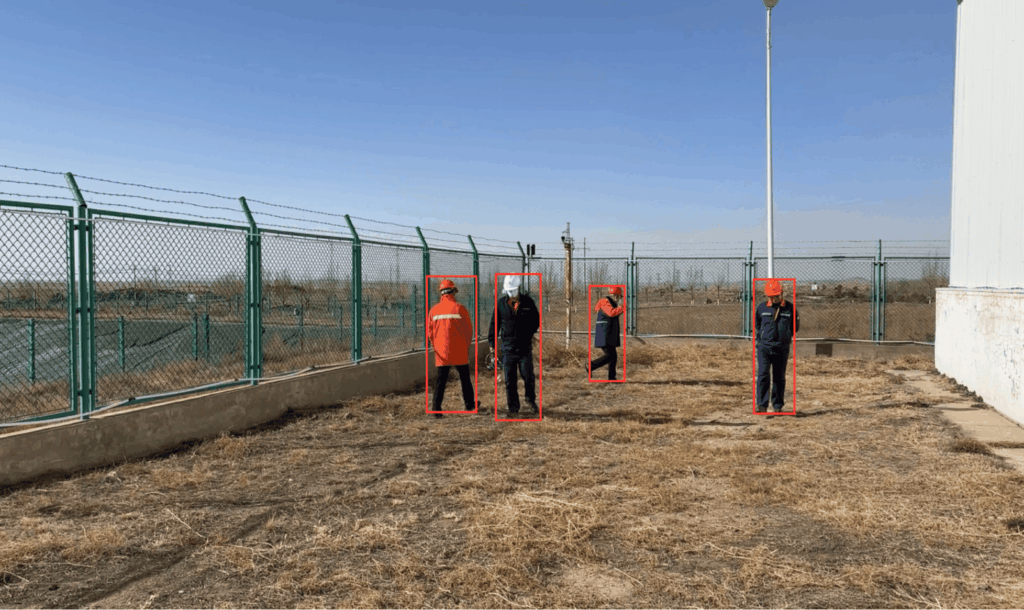
The monitoring system detected that a worker was on patrol.
The monitoring system detected workers who were not wearing helmets and protective equipment correctly.
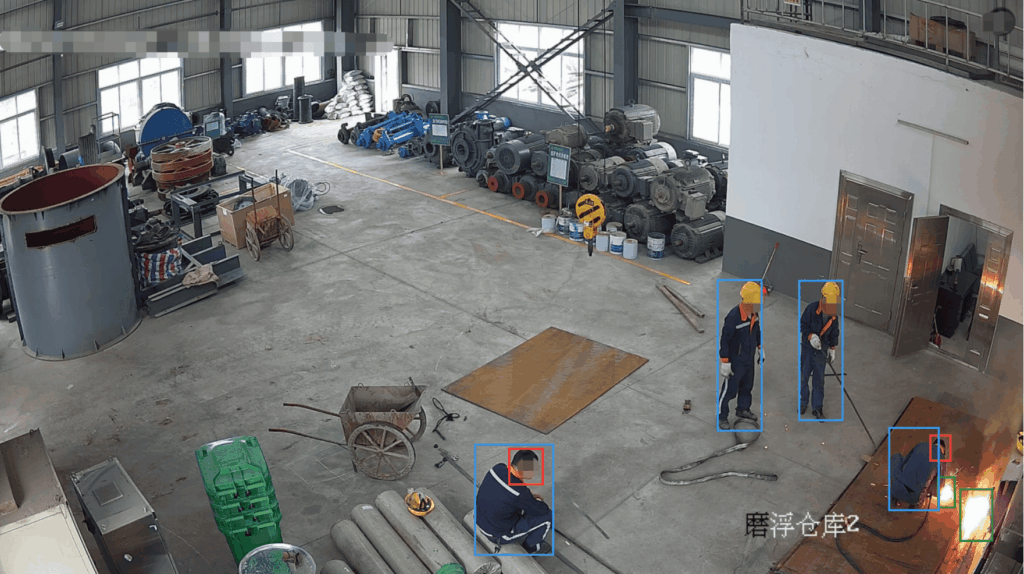
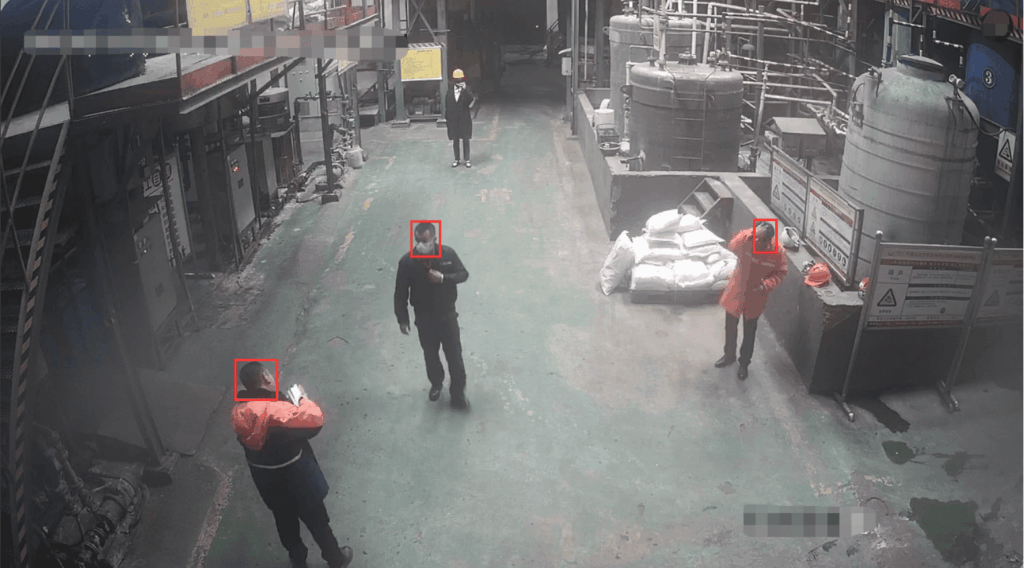
The monitoring system detected that the workers were not wearing safety helmets in the factory.
Conclusion
Our intelligent factory solution is centered around a multi-functional visual AI model, precisely empowering workplace compliance management. The solution employs a variety of behavior recognition and target detection algorithms (such as safety equipment detection, area intrusion identification, fire alarm perception, etc.) to comprehensively cover all aspects of safety production; the deep learning algorithm ensures extremely high recognition accuracy, significantly reducing false alarms, and enabling reliable capture of high-risk violation behaviors; the deployed AI cameras and edge computing micro-servers work collaboratively to achieve the digital transformation closed-loop of “intelligent perception (real-time violation recognition) → immediate handling (sound and light alarm / equipment interlock) → efficient management (automatic work order closure)”, effectively promoting the upgrade of manufacturing from passive supervision to intelligent proactive prevention.