Express Delivery and Logistics
Background and Challenges
Core contradiction: The imbalance between the “fast turnover” characteristic of the logistics industry and the “strong safety” requirement. Traditional manual supervision cannot simultaneously cover the three dimensions of compliance (operational norms) + equipment safety (operating status) + regional protection (intrusion control). This has led to a continuous increase in risks of cargo damage, fines, and production suspension.
In an efficient logistics system, the safety of the park and the compliance of operations are directly related to the safety of goods, personnel protection, and timely fulfillment of contracts. However, the traditional management model relying on manual inspections and passive monitoring is facing severe challenges:
Solution
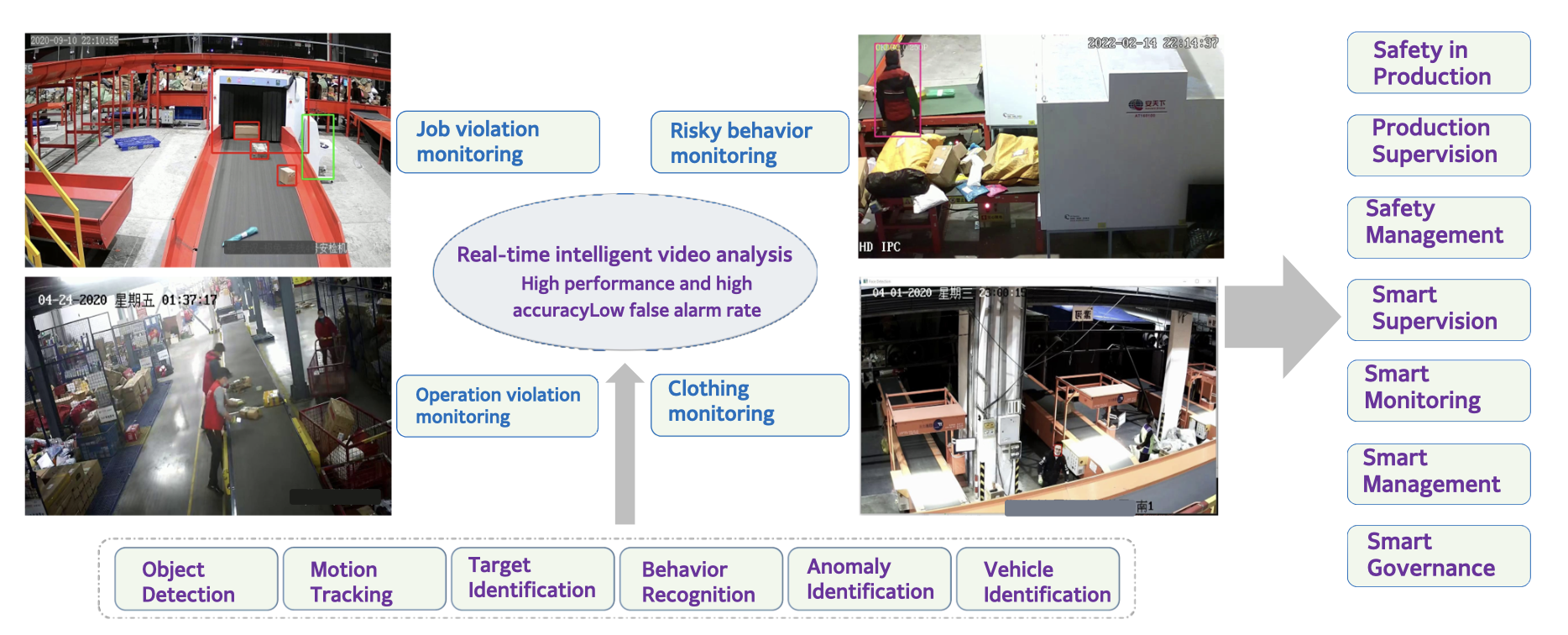
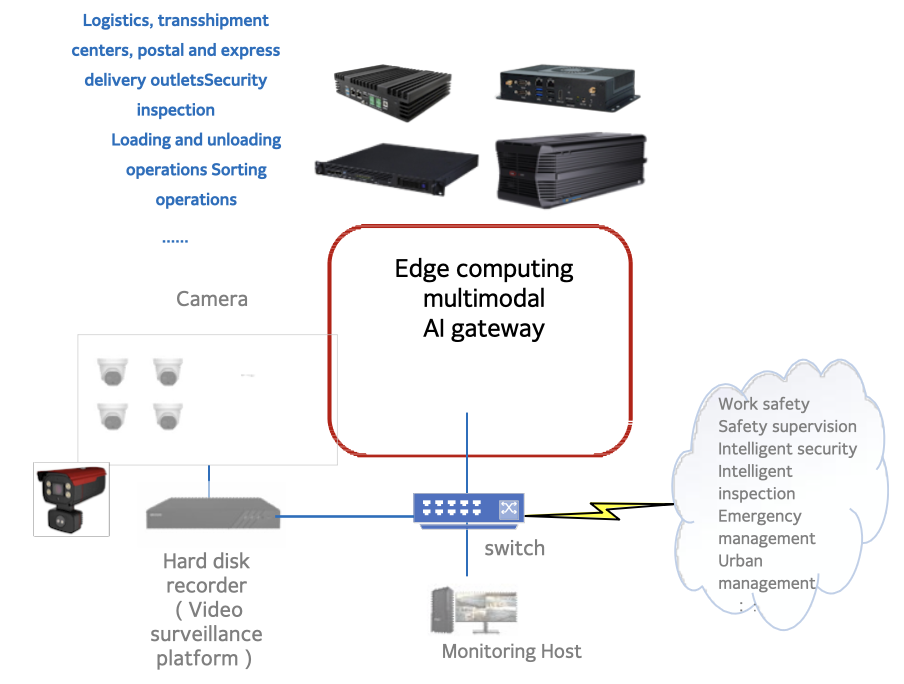
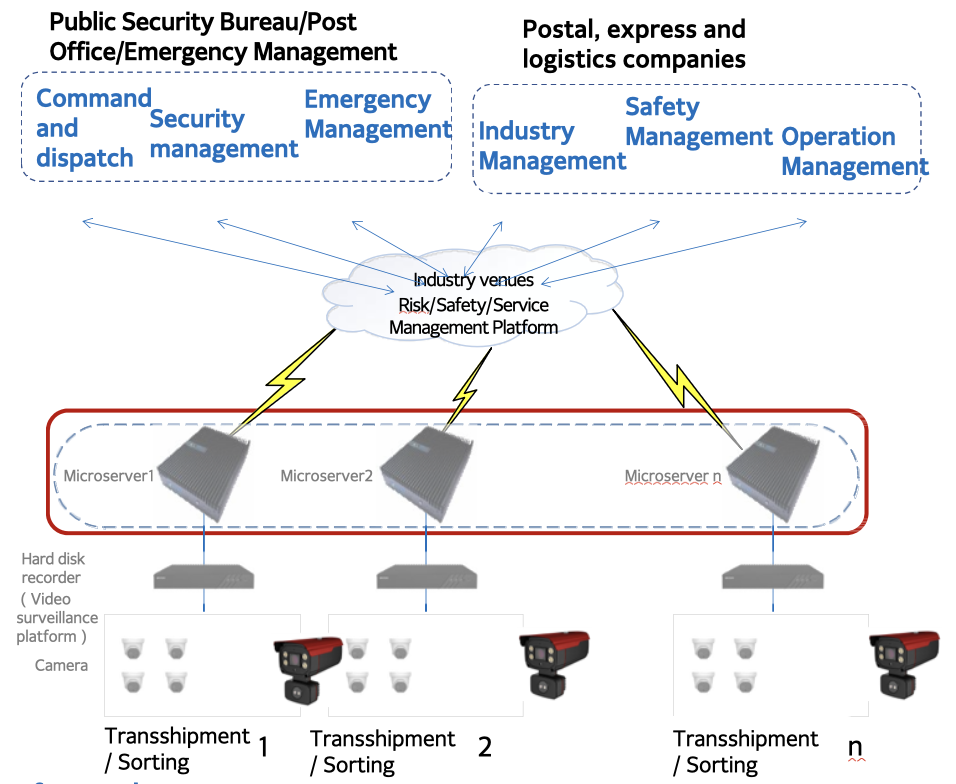
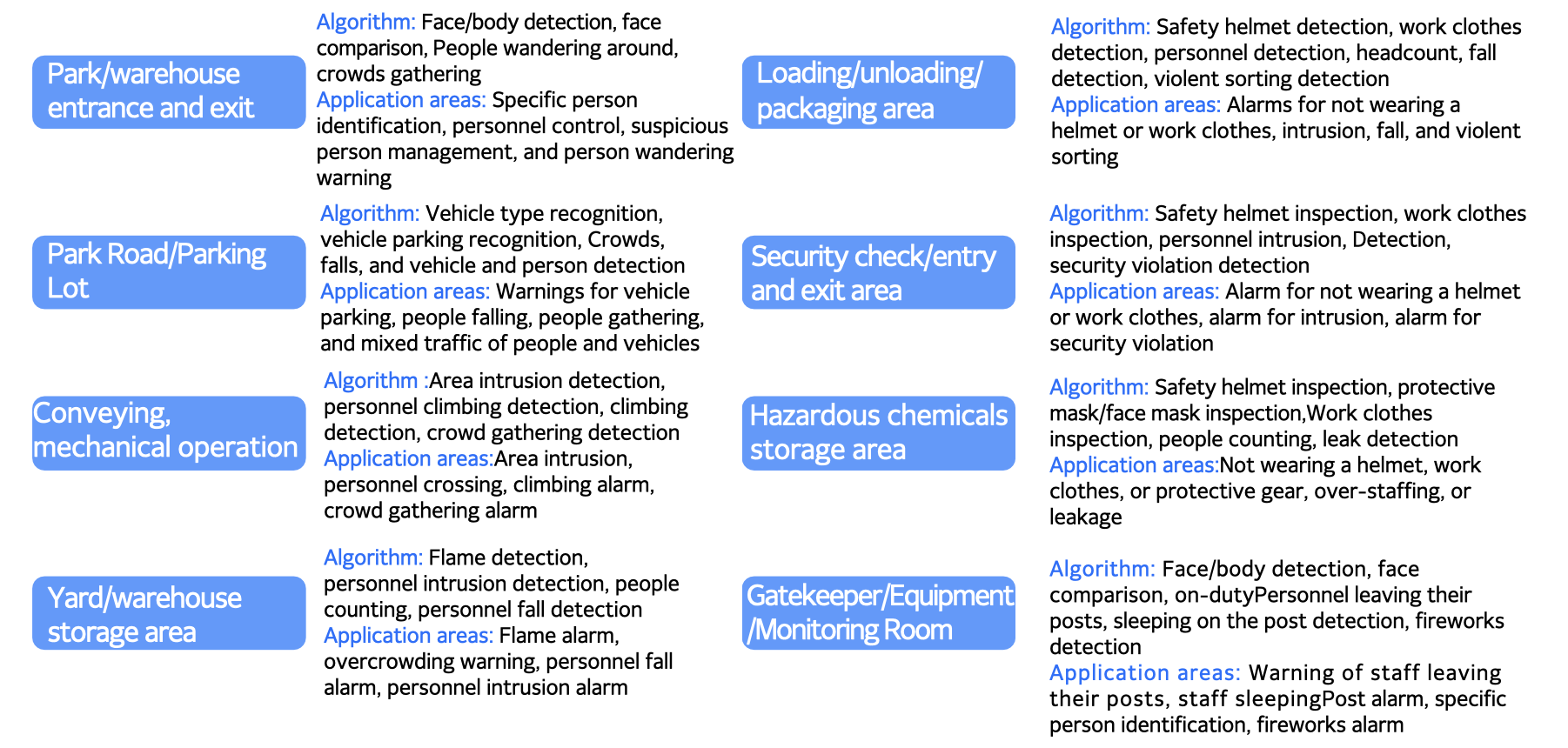
Monitoring Screenshot
The monitoring system detected the packages located on the conveyor belt and the operation console beside it.
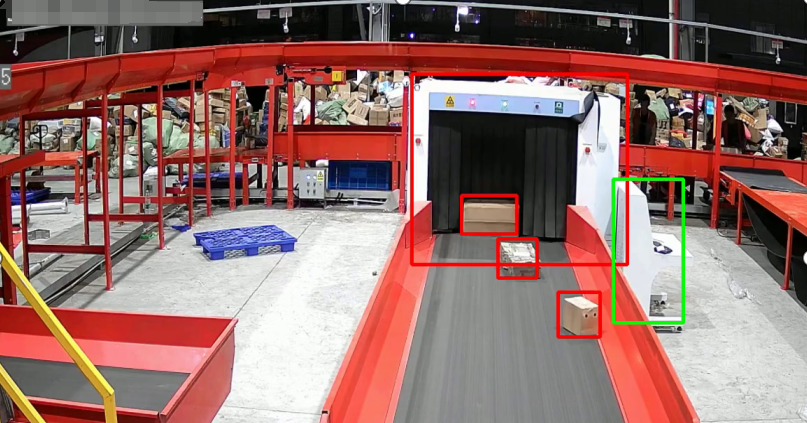

The monitoring system detected that a staff member was operating in violation of regulations: crossing the conveyor belt.
Result
This case covers multiple application scenarios, including security and intrusion detection, workplace compliance inspection, human flow and behavior analysis, etc. Through algorithms such as target detection, behavior recognition, and anomaly recognition, it realizes functions such as supervision of job violations, analysis of dangerous behaviors, and equipment operation monitoring, solving the problems of low efficiency and slow response of traditional manual inspections, and building an efficient and highly secure logistics industry monitoring system.